Detecting Surface and Slightly Subsurface Discontinuities in Ferroelectric Materials
Magnetic Particle Inspection (MPI) is a non-destructive testing method used to detect surface and slightly subsurface flaws in ferromagnetic materials such as iron, nickel, cobalt, and their alloys.
The process involves magnetizing the test object and applying fine magnetic particles over the surface. If a defect is present. such as a crack or void, it disrupts the magnetic field, causing magnetic flux leakage. The particles gather at the flaw, forming a visible indication.
B.E.C.A’s trained technicians analyze these indications to determine the size, location, and severity of the discontinuity, helping clients make informed maintenance and safety decisions.
MPI is commonly used on:
- Welds
- Pipes and fittings
- Castings
- Structural components
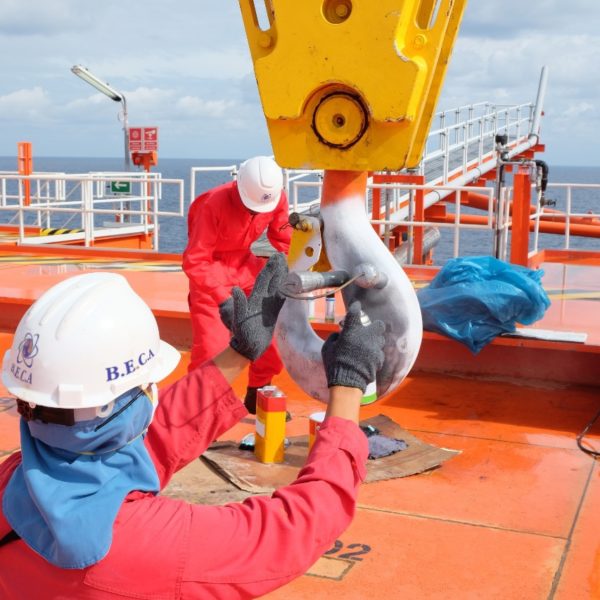
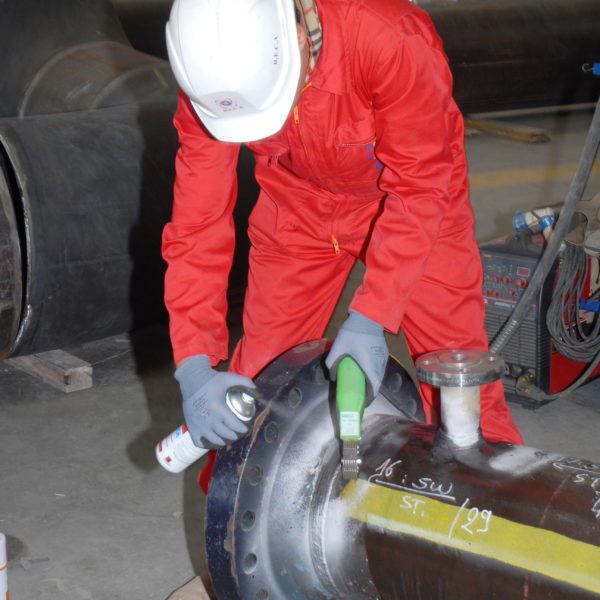
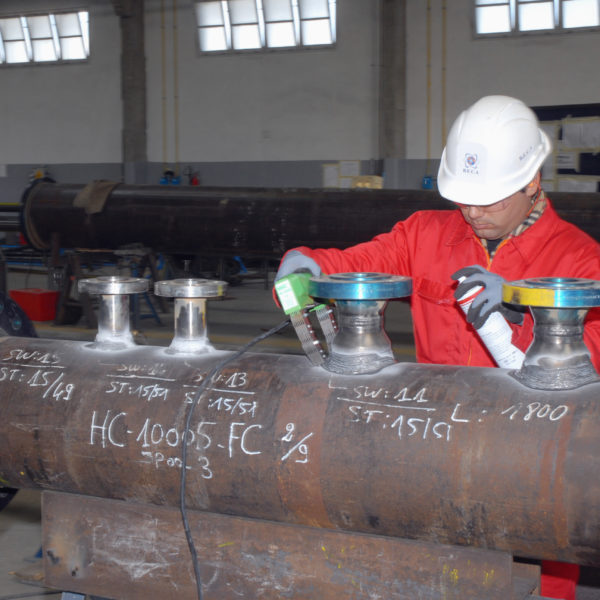
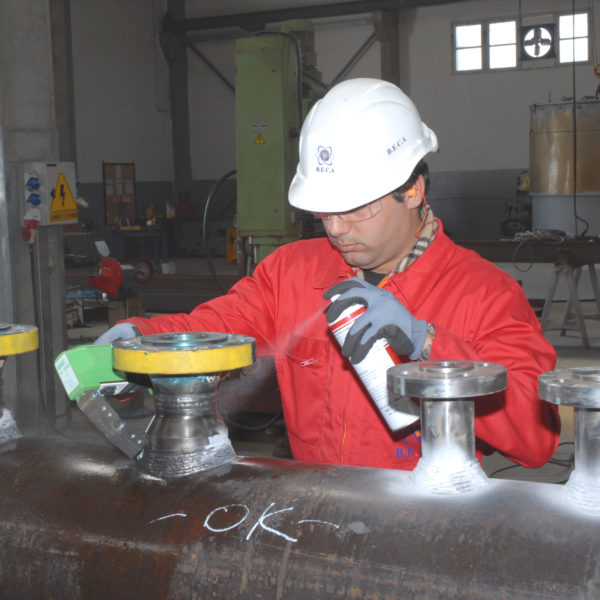
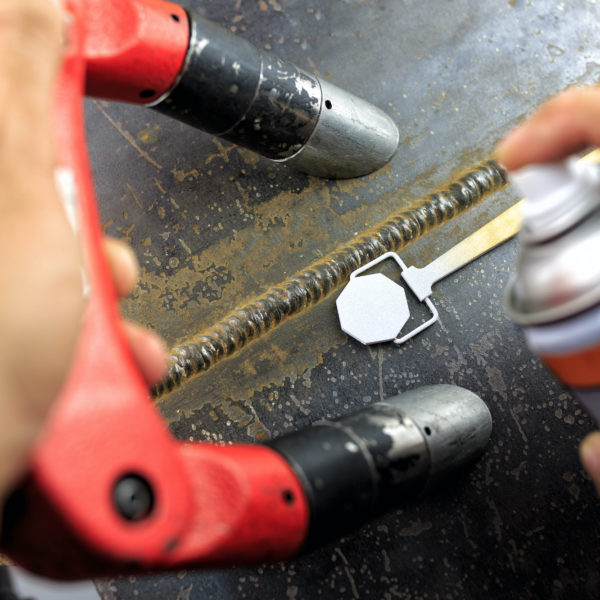

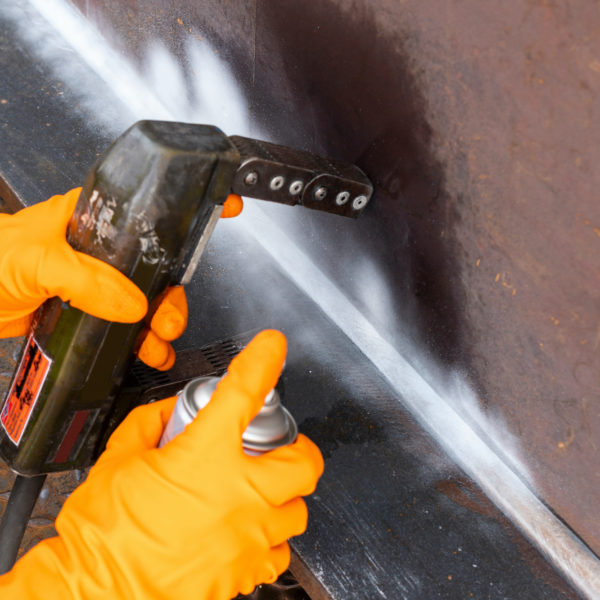