Manual and semi-automated ultrasonic corrosion profiling is used to create high-resolution maps of wall thickness and detect localized defects in pipes, tanks, and pressure vessels. This technique is especially effective in areas where fully automated scanners are not practical, such as small-diameter piping, vertical surfaces, or complex geometries.
Using dry-coupled ultrasonic scanning, operators can generate real-time B-scan and C-scan images, allowing the detection of corrosion, pitting, wall thinning, and weld defects — even through coatings and without surface preparation.
Advanced imaging features, such as stacked B-scans, make it possible to assess defect depth, orientation, and even detect misaligned or stepwise cracking. These systems are well-suited for inspections on hot surfaces, rough environments, and a wide range of shapes, from tight-radius piping to large flat panels.
Benefits of Ultrasonic Corrosion Profiling:
- High-resolution thickness measurements with scan grids as fine as 0.5 mm
- Real-time B-scan imaging for accurate corrosion detection and defect sizing
- Operates on materials up to 150 mm thick and at temperatures up to 200°C
- No paint or coating removal required
- Reduces reliance on scaffolding through remote access capabilities
- Compatible with digital inspection management systems
Applications:
- Inspection of piping, tanks, and pressure vessels
- Corrosion under insulation (CUI) assessments
- Weld overlay monitoring
- Slug catchers and crude oil transfer lines
- General corrosion mapping for RBI programs

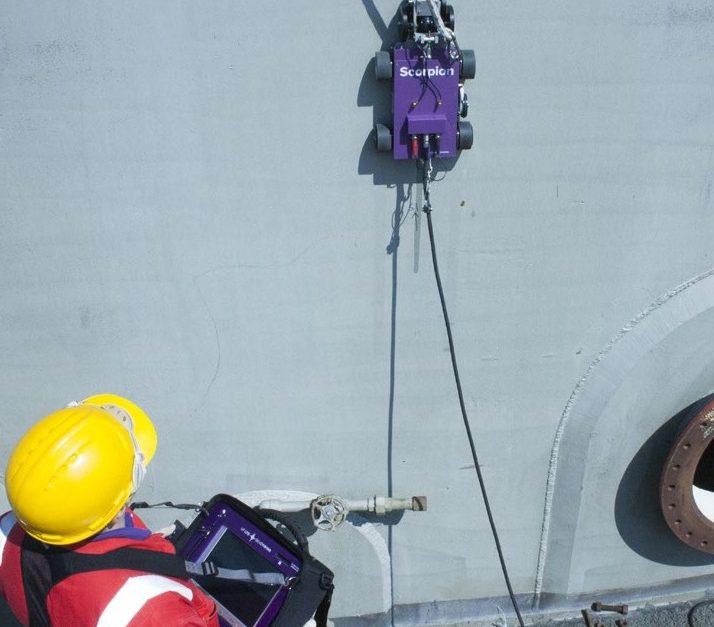
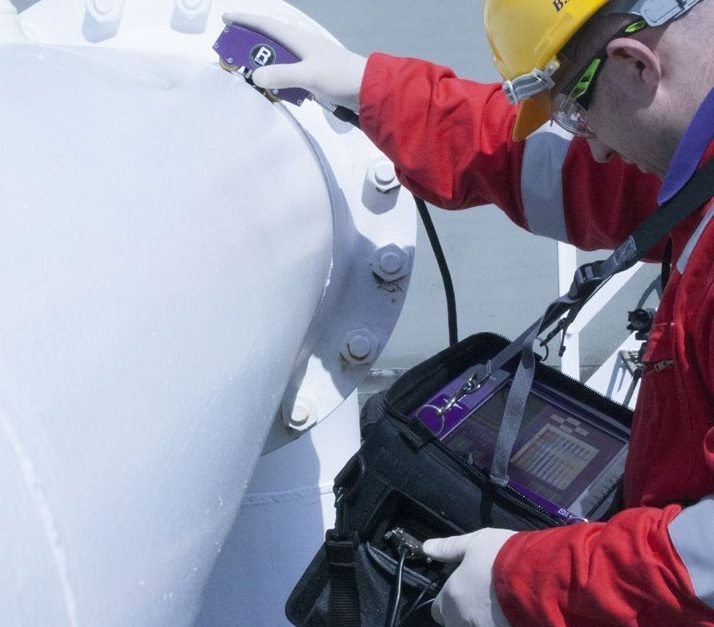
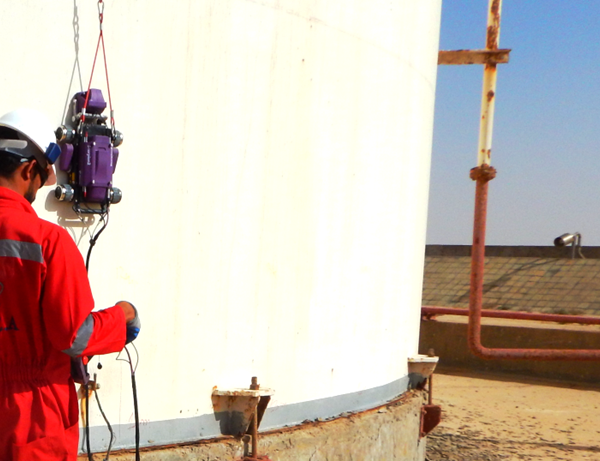

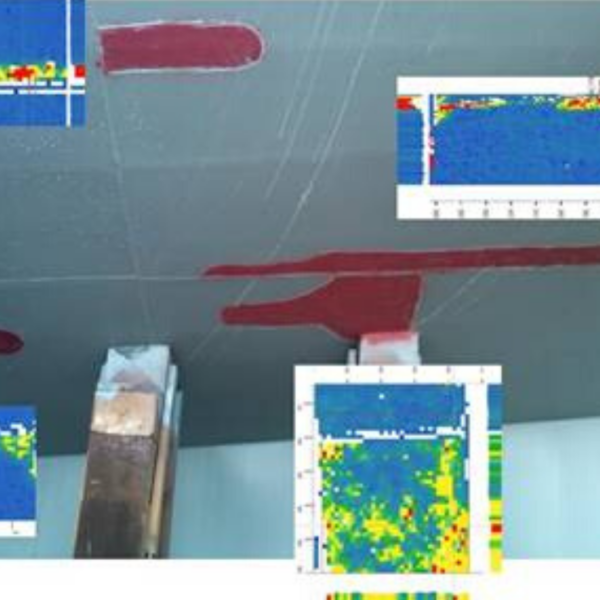
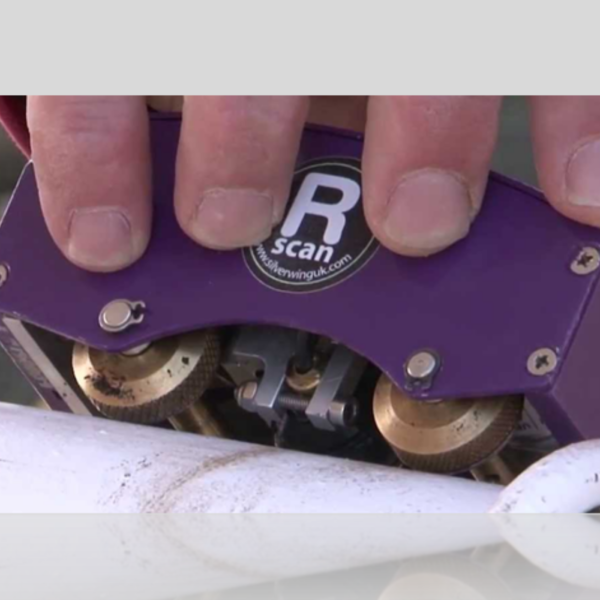
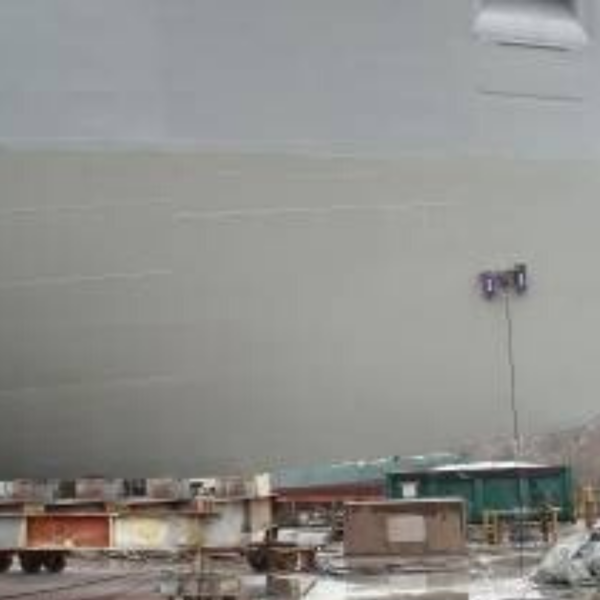